Online cell culture in CGMP
Radio Frequency Impedance (RFI) has been used successfully for monitoring and controlling animal cell processes at a production scale. Different options for transmitters are available for such cGMP applications. A transmitter with a touch screen interface, the Aber V350 can be installed next to the bioreactor (Figure 1).
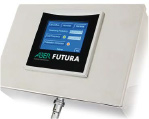
Figure 1 – Aber V350 transmitter
Alternatively, the single or multi channel Connect Hub which does not have a screen can also be integrated into control systems. The availability of single use RFI probes has opened up many more options for future applications.
In many cell culture manufacturing processes it is traditional to define a fixed-volume feed strategy for nutrient feeds based on historical cell demand. However, one major drawback of this strategy is that once the feed volumes are defined, they are inflexible to batch-to-batch variations in cell growth and physiology. This can lead to inconsistent productivity and product quality. An auto feedback system using online Aber RFI measurements makes it possible to automatically control the complex feed rates (Zhang et al., 2015). The nutrient feed amount can be determined by calculating the integrated biomass which is derived by determining the area under the bio-capacitance (BC) curve across a predetermined time interval (typically 24h).
The original approach in the study by Zhang et al. (2015) was to convert the BC reading to VCD and then feed based on the estimated cumulative of estimated cell growth (cICG). However, the capacitance reading was found to directly correlate with the cICG-based feed amount which made it feasible to directly use the online BC reading to control the feed rate. This also eliminates the need to use models based on either the Cole-Cole equation-based approach or multivariate analysis (Lee et al., 2015) to adjust capacitance to match the offline viable cell density (VCD) during the later stages of cell growth, where there may be a divergence observed between the measurements.
Summary of the benefits
- Utilize real time cell density measurement technology in cGMP manufacturing
- Obtain complete certification package, including IOQ’s
- Monitor cells in situ and in real time in a variety of bioreactor platforms (reusable and single use)
- Utilize direct integration to transfer important system information for batch records.
- Eliminates/reduces need for sampling
- Reduced operator efforts
- Reliable system check procedures
- Perform cell density measurements non-disruptively
- Obtain fingerprint of the process in real time
- Can be used to measure a variety of processes – batch, fed batch, perfusion, continuous processes
- Troubleshoot the process
- Control critical events during the process
- Consistent transfer of biomass from one vessel volume to the next
- Better process time planning
- Automatic cell concentration control
- Automatic complex nutrient feed control
- Improve productivity and process consistency
- Work with experts in the technology for effective support
References
Lee, H.W., Carvell, J., Brorson, K. and Yoon, S., 2015. Dielectric spectroscopy-based estimation of VCD in CHO cell culture. Journal of Chemical Technology & Biotechnology, 90(2), pp.273-282.
Zhang, A., Tsang, V.L., Moore, B., Shen, V., Huang, Y.M., Kshirsagar, R. and Ryll, T., 2015. Advanced process monitoring and feedback control to enhance cell culture process production and robustness. Biotechnology and bioengineering, 112(12), pp.2495-2504.
Fernandes, J., Currie, J., Ramer, K. and Zhang, A., 2018. Development of Capacitance Tools: At-Line Method for Assessing Biomass of Mammalian Cell Culture and Fixed Cell Calibration Standard. Biotechnology Journal, 14(4), p.1800283.
Ma, F., Zhang, A., Chang, D., Velev, O., Wiltberger, K. and Kshirsagar, R., 2019. Real-time monitoring and control of CHO cell apoptosis by in situ multifrequency scanning dielectric spectroscopy. Process Biochemistry, 80, pp.138-145.
Moore, B., Sanford, R. and Zhang, A., 2019. Case study: The characterization and implementation of dielectric spectroscopy (biocapacitance) for process control in a commercial GMP CHO manufacturing process. Biotechnology Progress, 35(3), p.e2782.
Book your no obligation evaluation
Seeing is believing. Experience the advantages
of using bio-capacitanceto measure viable
biomass in 3 easy steps!